IBC Tote Filling Machine for Bulk Liquid Packaging_
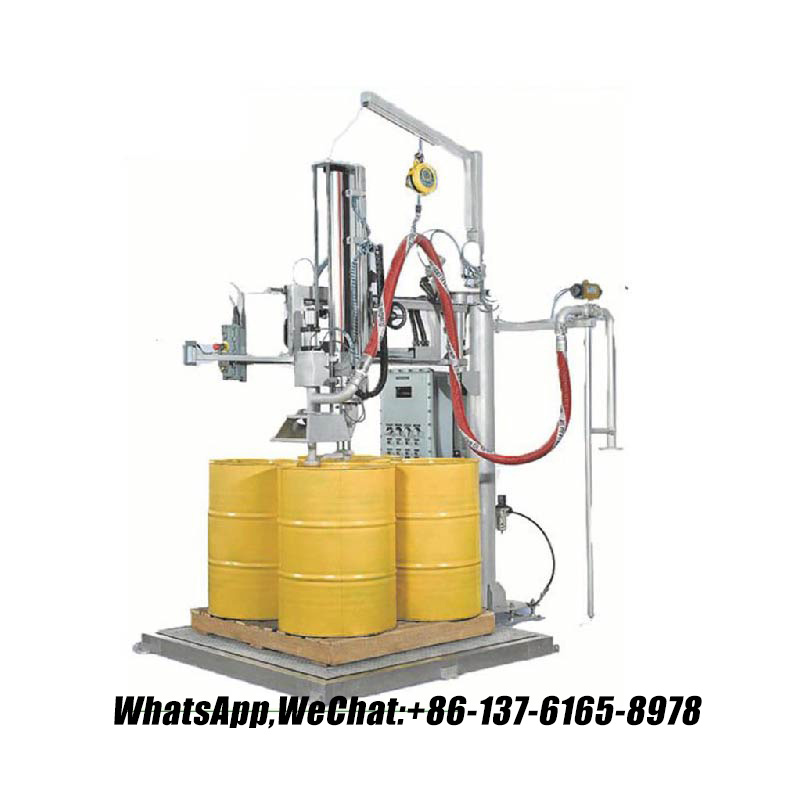
The IBC Tote Filling Machine for Bulk Liquid Packaging is a specialized system designed to efficiently and safely fill Intermediate Bulk Containers (IBCs) with liquids, chemicals, or bulk products. Below is a detailed overview of its features, applications, benefits, and technical specifications.
Key Features:
High-Capacity Filling:
Designed for filling large volumes (e.g., 1,000 to 3,000 liters per IBC).
Suitable for bulk liquids, chemicals, oils, solvents, and food-grade products.
Precision and Accuracy:
Weight-Based Filling: Integrated load cells ensure accurate fill volumes with ±0.5% accuracy.
Level Sensors: Radar or ultrasonic sensors detect liquid levels for precise filling.
Anti-Foam Design: Minimizes air entrapment and foaming during the filling process.
Safety and Compliance:
ATEX/IECEx Certified: Explosion-proof design for hazardous environments (Zone 1/21 or Zone 2/22).
Corrosion-Resistant Materials: Made from 304/316L stainless steel or optional PTFE/epoxy coatings for aggressive chemicals.
Emergency Stop Button: Immediate shutdown in case of emergencies.
Overfill Protection: Prevents overfilling of IBCs, reducing waste and spills.
User-Friendly Interface:
Touch Screen HMI: Intuitive interface for programming, monitoring, and adjusting filling parameters.
Multiple Product Profiles: Stores settings for different liquids, IBC sizes, and fill volumes.
Modular and Customizable:
Adjustable Nozzles: Fits standard IBC spouts (e.g., DN50, DN65) and can be customized for specific containers.
Scalable Design: Can be upgraded with additional modules (e.g., labeling, capping, data logging).
Efficiency and Automation:
Fully Automatic Operation: Reduces labor costs and minimizes human error.
Drip-Free Valves: Prevents spills and ensures clean, precise filling.
Vacuum Filling Option: For handling viscous or foaming liquids without air entrapment.
Environmental Protection:
Vapor Extraction System: Captures and vents hazardous fumes during filling to protect operators and the environment.
Spill Containment: Optional drip trays or catch basins to manage accidental spills.
Durability and Low Maintenance:
Heavy-Duty Construction: Robust frame and components designed for high-volume use.
Easy Cleaning: Stainless steel surfaces and removable parts facilitate sanitation.
Applications:
Chemical Industry: Filling corrosive, flammable, or toxic chemicals (e.g., acids, solvents, oils).
Food and Beverage: Packaging bulk liquids like syrups, oils, or beverage bases.
Pharmaceuticals: Filling solvents, oils, or other pharmaceutical ingredients.
Agricultural Chemicals: Safely filling pesticides, fertilizers, or herbicides.
Oil and Gas: Handling fuels, lubricants, or petrochemicals.
Water Treatment: Filling bulk chemicals for water purification processes.
Benefits:
Efficiency:
Fully automated operation reduces labor costs and increases throughput.
High-speed filling minimizes production downtime.
Safety:
Explosion-proof design and corrosion-resistant materials ensure safe operation in hazardous environments.
Overfill protection and emergency stop features prevent accidents and spills.
Precision:
Weight-based and level-based filling systems ensure accurate fill volumes, reducing giveaway and waste.
Anti-foam design minimizes product loss and contamination.
Versatility:
Suitable for a wide range of IBC sizes and types (e.g., totes, tanks, containers).
Customizable for specific industry requirements (e.g., food-grade, hazardous chemicals).
Cost-Effective:
Reduces product waste, labor costs, and downtime compared to manual operations.
Minimizes cross-contamination risks with dedicated equipment.
Environmental Compliance:
Vapor extraction system ensures safe handling of hazardous fumes, protecting operators and the environment.
Modular design allows for future upgrades to meet evolving regulations.
Technical Specifications (Example):
Filling Capacity: Up to 1,000 liters per minute (adjustable)
Filling Accuracy: ±0.5% (weight-based or level-based)
Materials: 304/316L stainless steel (corrosion-resistant) with optional PTFE/epoxy coatings
Power Source: Electric (220V/50Hz or 110V/60Hz) or pneumatic (optional)
Safety Certification: ATEX, IECEx, CE, FDA (depending on configuration)
Dimensions: Compact footprint (e.g., 1500mm x 1000mm x 2000mm)
Weight: ~500 kg (depending on configuration)
Touch Screen: Color LCD with user-friendly interface
Optional Add-Ons:
Conveyor System: Automated transport of IBCs for continuous operation.
Labeling Machine: Automatic application of labels for hazard identification, expiration dates, or batch numbers.
RFID/Barcode Scanners: For automatic IBC recognition and tracking.
Data Logging: USB or Ethernet connectivity for recording fill data and integration with MES/ERP systems.
Vacuum Filling Module: For handling highly viscous or foaming products.
Capping Machine: Integrated tamper-evident or hermetic capping for sealed IBCs.
Vapor Extraction System: Filters and vents hazardous fumes during filling.
Conclusion:
The IBC Tote Filling Machine for Bulk Liquid Packaging is a reliable, precise, and efficient solution for filling large volumes of liquids in IBCs. With its advanced features, safety compliance, and customizable options, it minimizes labor costs, ensures accuracy, and enhances safety. Whether you need a basic system or a fully customized solution with advanced features, this equipment is a valuable investment for streamlining bulk liquid packaging operations.
Immediate Order:
Website: http://m.xtsy120.com/product/drumfillingmachines-en.html
China Manufacturing Co Ltd.: https://fillingmachinecn.en.made-in-china.com
-
High-Precision Customized Semi-Automatic Chemical Liquid Weighing and Filling Machine for 100L-1000L[2025-04-09]
-
200L Drum on Pallet Fully Automatic Bitumen/Asphalt Filling Machine[2025-04-16]
-
Automatic Mouth-Finding Filling Machine Is Suitable for Ink Solvent/Polyurethane Filling[2025-05-07]
-
55 Gallon Drum Filler for Chemical Petrochemical Food Agrifood Industry[2025-04-15]